How to Design and Build a Combat Robot - most popular sex toys
by:KISSTOY
2020-10-16
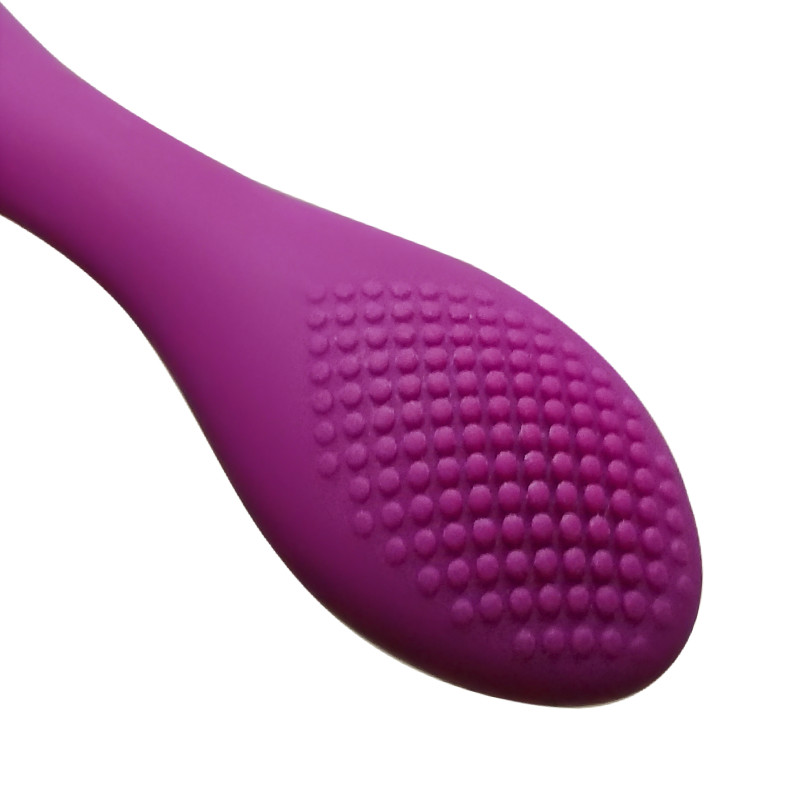
* Note: since the combat robot is back in the air on ABC, this instruction has gained a lot of traction.
Although a lot of information here is still good, please know that this movement has changed a lot in the past 10 years * combat robots have been very interesting since they became popular in the comedy Center.
Not long ago, I accepted the challenge of building several combat robots (
A 30lb and a 220lb).
Regardless of the size of the machine, the steps in the process are the same.
This Instructure will guide you through these steps and provide you with the resources to help the machine, and take my 30-pound robot as an example to understand what is involved.
The first step in building a robot is to think about what kind of robot you want to build.
When I start this project, I always look at what people have done and learn from what others have learned over time.
The Builders database is a great place to start your research.
Most competitions are signed up using this website.
One of the requirements of this site is that each team/robot has a profile with photos of the robot.
Because of this, you can easily browse hundreds of other robots in your weight level.
Another good starting point is to determine how much you are willing to invest.
Unless there are a lot of parts around you that can be reinstalled
Used from other projects, you need to consider any project from motor to material and don't forget the processing/construction time.
Below is a list of components that most combat robots usually need.
The main reason setting a budget is important to your project is that you can easily spend hundreds or even thousands of dollars quickly.
Robots are an interesting hobby that can meet any budget if you plan.
The last thing anyone wants to do is to get into the building and then not be able to do it due to funding.
Common components: * Drive Motor/transmission * wheels * chassis material * weapon Motor * speed controller for each motor * radio control system (
Receiver and transmitter)
* Battery * wire * main power switch * bearing * shaft and axle * screws and fasteners * armor material * weapons (
Material or purchase)
Don't forget that the spare parts are also important because you will damage the parts and parts during the battle.
In addition, competition requires at least two sets of batteries. It all starts with some sketches and some different concepts.
I always do some concepts and some initial layouts so I can determine the best design.
In addition, the more layouts completed before the final design, the easier it is for machining to transition to computer design.
This is one of my personal rules, when I start thinking about a design, I look for a robot that does something like that and try to see what is successful and what is unsuccessful, so I am in the design concept.
I have been thinking about two things: 1)
Is this robot different?
Does it have a wow factor? Will I be happy with it as a personal product?
How easy it is to maintain.
Do you need a complete disassembly to replace the frying motor
Assembly of robots?
Can I replace the parts in 10 minutes
15 minutes if needed?
These two key concepts help you focus when thinking about robots.
Also make sure you check the rules of the game you are considering.
Most activities use rules that are managed by the robot combat Alliance ()
But some organizations, such as combat robots ()
There are some different rules.
These rule sets will determine the type of machine you can build and how you can make them safe.
The last part of the initial design is to find out which parts you have to work on and make a quick layout of your basic overall size, with weight limits for each subsystem.
The more plans you make at this stage, it will help.
Each robot is made up of components made and purchased.
For a successful robot, it is critical to choose the right components.
In this step, I will introduce some of the main components of small and medium sized robots and how you can choose the one that suits your robot.
Car: The driving force behind any size robot you make.
They will move your robot and will power your weapon in many cases.
The motor used in the combat robot is a DC or DC motor designed to be used anywhere between 3 and 72 volts.
Like other components, you need to make a decision to choose the right one.
Four features to consider for each motor are torque/speed, voltage, size and weight.
Motor torque is usually oz-in or in-
Pounds in the "booth" area.
Since the DC motor generates maximum torque with minimal RPM blocking torque, this is just a reference point.
I only use torque as a comparison benchmark for different motors and try to get maximum torque under other constraints.
Because the larger the shape of your robot, the greater its weight.
When defining the size of a bot, try to make it as small as possible without sacrificing functionality.
Voltage is one of my last priorities, most motors are 12 V, but for those motors that are not just 12 V, you just need to make sure your electronics are voltage with the motor
12-common Motors
30 pound robot: drill motor-
Discount Tools store cheap drill bits for port cargo are stripped out of the housing and installed on the drive.
Many people also use the battery pack of these drill bits.
While cheap exercises are common, many people will spend extra money on high-quality exercises such as those made by DeWALT. Banebots -
Banebots is a company founded a few years ago with the sole purpose of providing parts for combat.
They have a large number of motors and transmissions that can be used out of the box.
For the convenience of not having to modify the drill bit to get the motor, I chose these for my robot, the old 36mm series (which I used)
It's easy to go bankrupt, but I have good results for the new 42mm.
Cars: There are all kinds of cars, and you can check many of them in the robot market. -
The wheels on the robot keep turning. . . .
In this part, the idea of not reinventing the wheel comes to mind, because there are many wheels of different styles in this sport.
The main question you need to ask yourself is if you want a live or dead shaft system.
In the live shaft system, the wheels are mounted hard on the shaft similar to the wheel of the car.
The challenge with this system is that now you need to install the bearing on the shaft and find a way to coupling the wheel to the shaft.
In a dead shaft device, the wheel rotates freely on the shaft, usually driven by a sprocket or belt connected directly to the wheel.
Although the system seems easier, it still has its own challenges, such as the need for a power transmission method (chain or belt)
Working better in small spaces where this size of robot directly drives the system.
The most common wheels used by most combat robots are made by colson, a soft polyurethane wheel that performs well on many different arena surfaces.
The main problem with these wheels is that they have no way to drive them for real-time axle applications.
For my robot I have custom hub on lathe but you can buy pre-
Make colson' with hubs in places like or hubs, you can use it to install some of the recently launched own wheels similar to colson', but I haven't seen or tested
Building materials
Small robots use a variety of composite materials such as carbon fiber and aluminum.
Just like any other part on your machine, each material has its pros and cons.
These are a few commonly used.
Aluminum: is an ordinary metal that is light weight, easy to form and process.
For these reasons, it is used on the chassis of most machines.
There are many different alloys for aluminum, but the most popular one is 6061-
After heat treatment, it is suitable for machining and welding.
This alloy can be soft and not very large against bump, so use it for components that do not see direct contact.
7075 is another major alloy, which is harder for one material, which makes forming and welding more difficult, but has better impact resistance. UHMW -
It is a durable plastic that is usually used as a stand for internal components.
Although it is a bit of a concession, it is still in good condition in the competition.
Even hand tools are easy to form. Polycarbonate -
Or the well-known lexan is a transparent and durable plastic that is largely impact-resistant and lightweight.
It is heavy per pound compared to aluminum, but it bends and bounces, not deformed like metal.
It will crack and break under extreme shocks, so use it for the top panel, not the armor. Titanium -
Armor is a good material, but the cost is too high, although many builders still use this material on high-end machines.
For my robot, I use 6061 and 7075 aluminum.
Mainly my stand and chassis 6061, my outer frame stand 7057.
I used a live shaft unit with a banebot 12:1 transmission to power 3 "x 7/8 coloson wheels with a custom hub.
CAD is the system used by all professionals to create products that you see and use every day.
It allows you to make 3D computer renderings, and before you build, see how things are combined on your computer.
This step may cause potential problems with your robot, thus reducing your time and cost.
It is generally believed that CAD systems are difficult to use and build if you are not an engineer or have been trained in the use of some courses.
Recent CAD software has shifted from five years ago so that they can build models with a UI that anyone can pick up and learn in a few hours.
The three most popular software in the industry are Autodesk Inventor, Solidworks and Pro-e.
Each has its own advantages and disadvantages, but they are comparable for this type of design.
I won't discuss how to use CAD in this Instructure, but there are a lot of resources available online to use this type of software.
Buying CAD software can be very expensive, but fortunately, there are a lot of opportunities for free software licenses if you are a student, or if your company has a software license.
Students can get autodesk inventor free of charge from the email you need
Edu endingYou can also get a copy of solidworks's very cheap/free student version from time to time online.
They also have a good tutorial on robot design here.
I suggest that both Inventor and Solidworks provide a simple interface, and more importantly, there are many models that can be downloaded for free.
Stock parts such as bearings, screws, motors can be found.
Using these models can save time for modeling.
The most important thing about CAD design is that your size is correct.
Now it seems like a direct suggestion, but I see a lot of people trying to make realistic renderings and spending too much time making their parts look good, instead of focusing on real target CAD to make accurate models.
I will leave this step because the process steps for software design will become more obvious if you take the time to learn CAD.
If you choose to skip this step because you can't run the software or lack of interest, I recommend using the "cardboard template" method.
Before cutting the real material, take the cardboard and cut the scale model of each part for layout.
In web show, a good example of this method is revis3, which is called CUCM, located here. The purpose of this design step is to minimize costly errors. materials.
Additional instructions: * Modern CAD software can assign weight attributes so you can know how much weight your robot should have before building * Make sure you have adjusted the size correctly, so that they can, for example, the 1/2 "shaft will not be able to pass through the 1/2" hole.
For accurate processing, you have to deal with thousands of inches (. 001").
Depending on the design and number of resources you can start building parts.
There are many ways to do things, manual tools (
Puzzles, hammers, etc)
Hand workshop lathe, full cnc;
Which method you choose can ensure your safety.
If you are building a budget robot, it is likely that you will use manual tools or light power tools.
This is the way robots use more than other robots.
The only advice I can provide is to take a moment and use the template or CAD drawing you created to help with the process.
When I can't use the machine store, one of my preferred methods for this is to make full-size drawings from CAD and paste them into the material and then cut the parts using these guides.
The next step for manual tools is the standard machine store.
If you can use a Mil or lathe, you will be able to create highly accurate parts.
These tools can be very dangerous if you don't know what you're doing, so make sure that supervision or proper guidance happens before you start.
If you want to go to the machine store, which is available in most towns, you should be able to open the phone book and get someone to help.
Sometimes they are willing to donate their time and sometimes you need to pay their time.
There are some great resources to help you make online in this era. and www. cncbotparts.
Both are good sources.
For many complex robots, advanced manufacturing can play a role.
Among my last few robots, I was lucky enough to get CNC (
Computer numerical control)
And the spray of my robot parts.
This makes it very easy to build components, but it makes CAD design more important for accuracy because any machine store will build what you give them.
If you follow this path, make sure you take additional steps to make sure your design is correct.
I will even go to someone else who knows CAD to review your design to make sure you don't ignore something.
During the process of building the Assembly, the test assembled the parts together.
Don't be surprised if you have to modify some of them, as they don't always fit.
Depending on how they are made, your parts will be assembled together in different ways.
Products manufactured in a machine store or CNC are likely to be produced along with the design, and the more they are manufactured, the more modifications you need to make.
Just make sure to use the montra "measure cut once twice" because once you cut off the material it's hard to make it grow.
The main advice in the process is that if you take the time, things will go smoothly and don't be discouraged.
Note: If threaded fasteners are used, make sure that high-quality fasteners are used.
Fasteners for large box stores (
Home Depot and Los)
The quality is not high.
I recommend ordering from McMaster Carr www. mcmaster.
Or other industrial dealers.
Robots without control are just a piece of art.
You need some way to remotely control each of your motors or subsystems so that you can safely leave the area and still enjoy the fruits of your labor.
Depending on the style chosen by the builder, the control system from the robot to the robot may vary greatly.
Some builders prefer to use mirocontroller (
A small computer)
Program their robots for special features or make it easier for them to drive.
The most common way to fight is to use a radio control system similar to an airplane model or a car model.
The basic principle of the system is that your radio system comes with a receiver with a different output or channel, each of which is a speed controller connected to these ports.
In order for each motor to have proportional control, the speed controller is necessary.
You can read more about their purpose and functionality, and the cabling connection is outlined in the photo below.
Each motor is connected to its own speed controller, which is connected to the power supply via a switch or splitter.
The speed controller also receives the signal in the form of PWM (
Pulse width modulation).
The signal is explained in the speed controller, which provides the correct voltage for the motor.
For the live wiring example, you can view the marked photos here. All speed controllers are equal and there are many different voltage and AMP levels to make sure the voltage and AMP levels you get match the motor of your choice.
The price of the controllers is directly related to the amount of amps they can handle.
There are many companies that produce the right speed controller.
For all my bots, I used the innovative first generation Victor series controllers, one of the best-selling controllers ever built like a stone.
They have a wide variety of motor controllers, but since I have no experience working with others, I would suggest checking out some other reviews, especially for very small people, when choosing a radio system, you can now be in PPM (FM), PCM, 2.
4 GHZ, 800 MHZ and 802.
Each has its advantages and changes the price of the system. PPM (FM)-
One of the oldest and cheapest tables, you can get the full setup below $50.
These disturbances are often very bad and regulated by the FCC.
There are different frequencies used on the ground, and some are used in the air.
Make sure there is one for ground use because it is illegal to use one for air. PCM -
It is a system similar to PPM, except that there are some systems that can connect the transmitter to the receiver, thus minimizing interference.
These are still under FCC regulations. 2. 4 GHZ -
Same frequency as many home phones.
This is a real digital system that does not allow any interference once the receiver is paired with the controller.
This is the most common system now and the one I use on small combat robots (spektrum D6).
These systems run for about $300, but once you have it, you can use it again and again. 800MHZ -
The innovative first micro-controller system uses a 800 MHZ system.
This allows programming of advanced features.
These systems cost up to $1200, mainly for large robots.
I recommend it if you can afford it.
I use this system on my heavyweight robot (220lbs)
Combat robots can use a variety of types of batteries.
Small robots usually use LiPoly batteries, which have the advantage of long life, light weight and powerful functions.
Prices for these packages are starting to drop, but still more expensive than other options.
The medium-sized robot uses the NiCad package, similar to the one in the drill battery.
These packages are proven systems and are relatively cheap.
You can get a lot of battery packs in different sizes, shapes and configurations.
Many online companies allow people to customize their packaging and build according to the order.
I recommend custom packaging for this typing robot tends to use sealed lead-acid batteries or NiCad packaging.
SLA batteries are cheap and easy to buy.
They are designed to be installed in any configuration and have multiple sizes.
Unfortunately, they tend to be heavier than their NiCad counterparts.
The battery was the last thing I chose for me because there were so many choices.
I calculated the amount of electricity I will use during the race, found the battery pack with the right capacity and fit the space profile of the robot.
Recently I have mastered some new lithium batteries and I will be experimenting for future machines.
Now that you 've put your robots together and connected, you 've reached the really interesting part. TESTING.
When doing so, make sure that you are properly protected and safe, depending on the size and weapon of your robot, and if not properly controlled, your robot can be fatal.
Before I test the robot together, I like to test the subsystem separately.
This way, I can analyze the problem of each component before I have to backtrack the whole machine to find the problem.
Once your robot is complete, be sure to drive your robot and feel the control, many games are won or lost because of driving skills.
The more you test before the game, the better your preparation will be.
I'm trying to break my bot before the race because when I have time to fix them instead of the time between races, I 'd rather find out the error and fix the problem.
Another benefit of running the machine is that every new gearbox or mechanical component must be slightly worn out and loose.
You want to try to break everything before the first race so that you don't deal with changing robot conditions all day long.
In the end, it is important to remember that design is an iterative process.
You will never get it right the first time, but you can get it to work by testing and modifying it.
Now that you have made a robot, be sure to have a good time.
Bring it to the competition and do your best to remember that there is no need for you to win every game or event because making machines is 75% + fun of the project.
Every robot you make will be a little better than the previous one and use them to improve your skills as a designer and engineer.
I hope you can find this helpful and informative note.
Here are other resources for bot Construction.
Battle Robot Forum :-
My new robot video show, more diy content and news (coming soon)
Source of parts and supplies: AndyMark. biz -
Mechanical components. com -
Market for cars, wheels and parts
All the metal you need
Metal suplusonlinemetals. com -
All kinds of metal. G. Micro -
Extra electrons, etc. SDP-SI -
Driver & H-
Integration of surplus electronics and mechanical and electrical
Spare electronic products, etc.
All electronic products
Spare electronic products, etc. Northern Tool -
Tools, wheels, chain drive parts
Industrial suppliersCarr -
Industrial supplier of Berg
US science & trade-precision gear products
Spare motor, battery, gear, pulley and?
Industrial metal supply
The balance of stock and steel and aluminum are traded heavily by pound.
Delta Engineering team
RC interfaces, motors, and other combat-specific robot parts. com -
A large collection of robots and electronic guides, novels, toys, etc.